- Supercool
- Posts
- đ Rare Earths, Recycled: Cyclic Materials Cuts Into China's 90% Head Start
đ Rare Earths, Recycled: Cyclic Materials Cuts Into China's 90% Head Start
We throw away the rare earth metals we urgently need. Cyclic Materials recycles them.
The Hidden Machinery Behind the Low-Carbon Future
At Supercool, our aim is to show you the low-carbon economy by spotlighting de-risked, data-backed climate solutions now scaling, so you can act on them with confidence.
While many proven climate solutions are visibleâsolar panels, wind turbines, batteries, e-bikesâmost arenât. Theyâre embedded deep in buildings, infrastructure, and machines.
Often, they hold the key to making the modern worldâand our path to decarbonizationâmove.
Behold, rare earth magnets.
Theyâre the force inside electric motors â powering EVs, spinning wind turbines, running the hard drives that enable enterprise data centers, and enhancing the images from MRI machines.
Weâre about to need a lot more of them.
By 2035, global demand for rare earth elementsâthe key ingredients for magnetsâis projected to surge as much as threefold.
Yet today, less than 1% of rare earth magnets are recycled. Making matters more challenging, China controls over 90% of the global supply.
The clean energy transition, geopolitical security, and economic competitiveness now hinge on access to these materials on a massive scale.
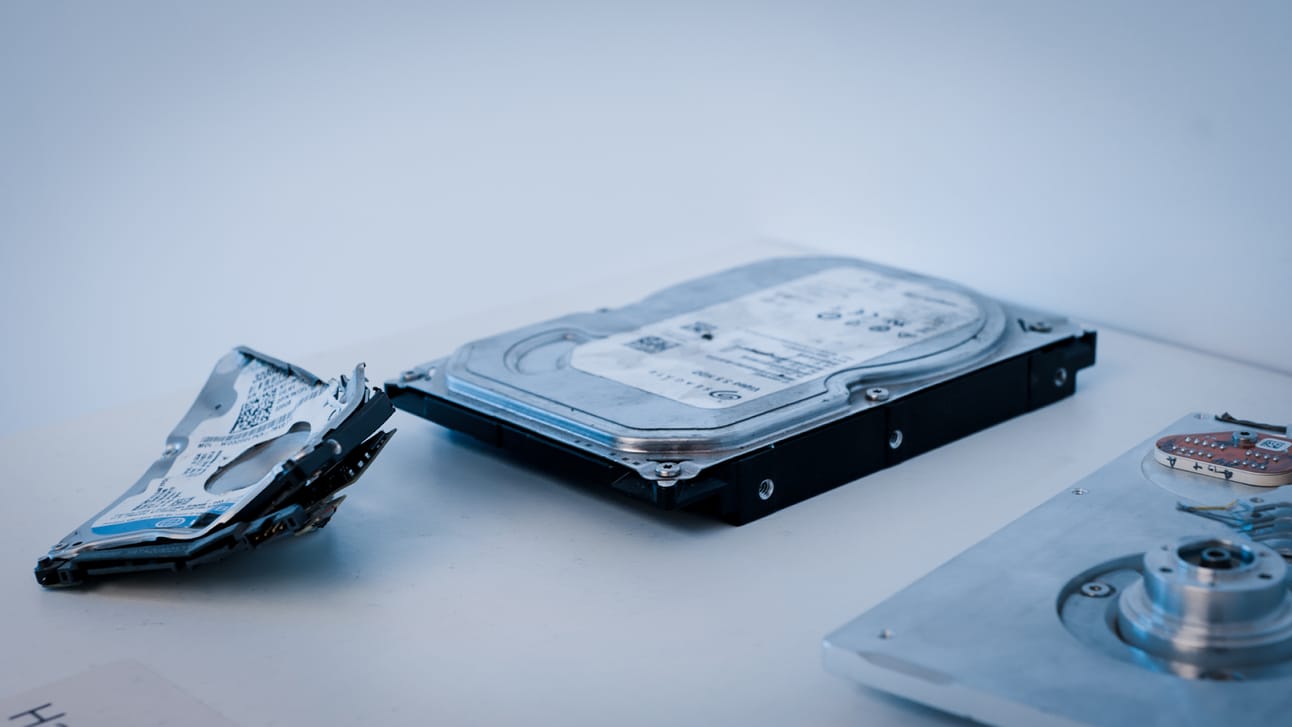
A hard drive containing rare earth magnets.
Rare Earth Metals Are All Around Us
Ahmad Ghahreman, co-founder & CEO of Cyclic Materials, spent his career as a metallurgist, mastering the making of metals, first as a mining executive, then as a university professor and lab director.
In 2020, he realized something few others saw.
âWe're going to need many of these metals,â he says. âAnd we recycle almost none of them. Those two statements made rare earth metals the most critical, least circular metals out there.â
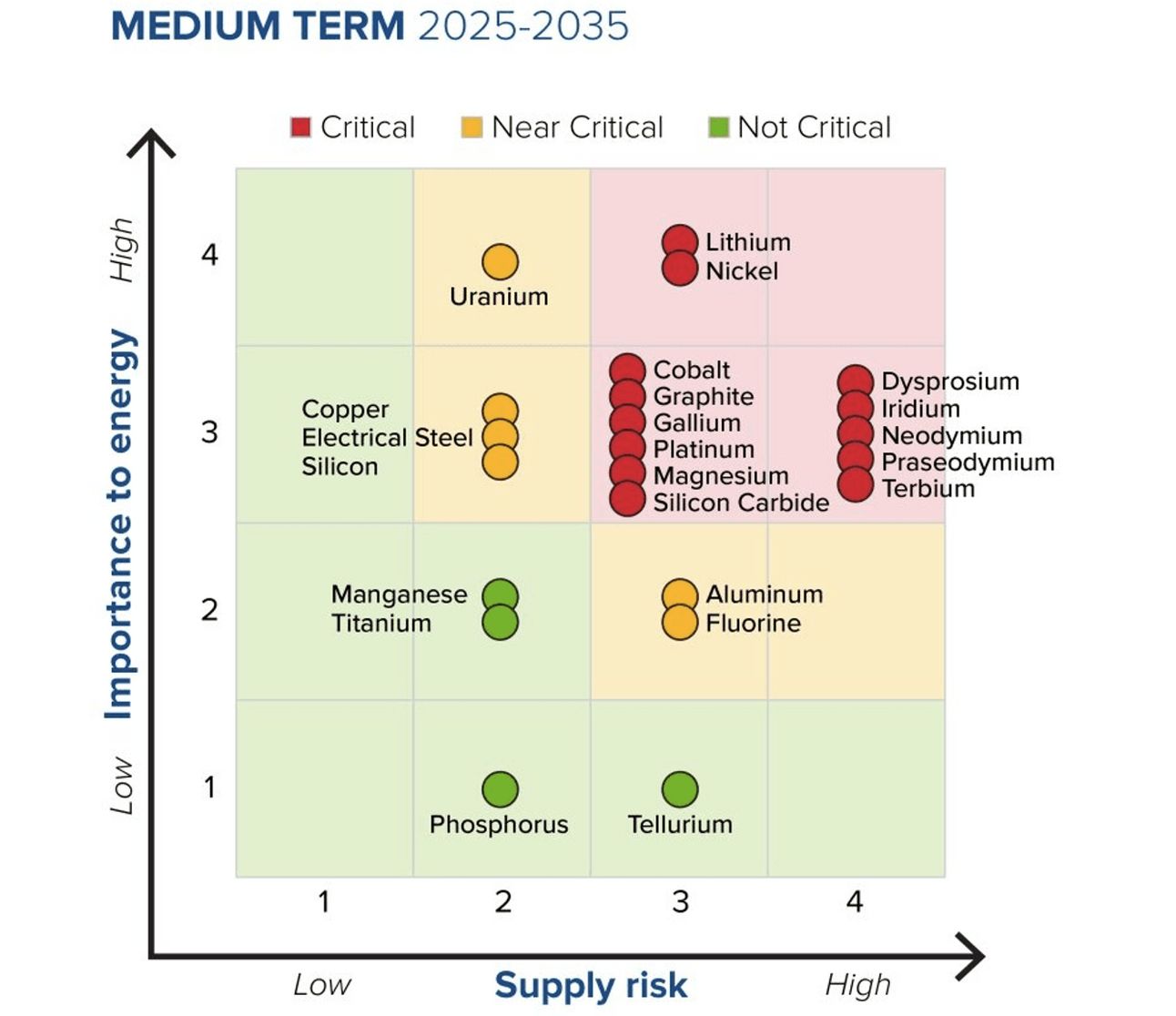
The criticality of various metals. On the far right in red are the most critical rare earth metalsâthese are used for magnets. Source: US Department of Energy
The insight behind Cyclic Materials was simple but powerful: Urban centers are massive above-ground mines for extracting rare earths.
China may control the virgin supply. The West controls the finished goods that contain them. Millions of electric motors in hybrid and electric cars, turbines, power tools, and appliances present an urban mining opportunity at civilization-scale.
But today, when those machines reach end-of-life, we throw the magnets away. They get shredded, melted, and lost forever in steel recycling plants. Or tossed in landfills.
âThese are the most valuable materials in the entire system,â Ahmad says. âThey have the highest carbon footprint when mined, and we still throw them out. It just doesnât make sense.â
Ahmad saw the opportunity to build the urban mining technology and infrastructure to harness these end-of-life resources. He launched Cyclic Materials to do it.
The Breakthrough: Separating Magnets from Steel
The breakthrough came by solving the industrial bottleneck that made recycling rare earth magnets impossible.
âMagnets being magnetic attach to steel,â Ahmad explains. âHand in hand with steel, they go to steel recycling plants. There, rare earth elements get locked into the slag phase. Itâs a stable glass-like phase â and once theyâre locked in, theyâre lost for good.â
Recovering rare earths after this point is technically possible but economically unfeasible. Cyclic Materials figured out how to intervene earlier.
âWe separate them with our technology just before steel heads to the recycling plant,â Ahmad says. âNow we have a solution that didn't exist years ago.â
That early-stage separation makes circularity possible for rare earths for the first time in history.
Once separated, Cyclic Materials uses a chemical process to purify the magnets into ultra-high-quality rare earth oxides, which are then turned back into metals and reenter the supply chain.
The environmental benefits are massive.
âFor the same amount of product, we produce only 35% of the carbon that mining would,â Ahmad says. âAnd we consume only 5% of the water.â
Spoke and Hub Logistics: Built for Urban Mining
Cyclic Materialâs supply chain is designed to recover rare earth magnets where people and, thus, end-of-life products are most concentratedâin and around cities.
Spokes: Collection points for end-of-life motors. Rare earth magnets are separated from steel. Then the steel, aluminum, and copper are sold to local recyclers, leaving behind the magnets.
Hub: The central processing plant that receives the magnets and recycles them into ultra-pure, high-quality rare earth oxides, ready to be shipped to customers and turned back into metals and eventually magnets.
âWe start by reducing end-of-life products to copper, aluminum, steel, and magnet,â Ahmad explains. âCopper, aluminum, steel â we sell those immediately. Only the magnet stays with us. And that small, high-value product goes to the hub for chemical processing.â
Proof on the Ground
In 2024, Cyclic Materials shipped its first ton of recycled rare earth oxidesâa world-first.
In April, the company announced that its first large-scale U.S. facility will be built in Mesa, Arizona, with the capacity to process 25,000 tons of end-of-life products per year.
For perspective: At its demonstration facility in Kingston, Ontario, Cyclic Materials can already process up to one ton of material per hour, the equivalent of recycling 10 to 15 Tesla motors.
The new Arizona plant will be eight times larger, and itâs the first of many planned across North America and Europe.
Some of the worldâs biggest companies arenât just investingâtheyâre placing orders.
Microsoft, Amazon, BMW, Jaguar, and others are backing Cyclic Materials as customers, investors, and strategic partners (In April, the company extended its $57 million Series B round to bring on Amazon).
As Ahmad says, âCompanies that have invested in us or partnered with us are driven by one of two things â or both. Environmental goals, or geopolitics.â
Environmental: Companies like Microsoft are pursuing zero-waste goals by 2030. A local, recycled supply of critical metals supports that mission.
Geopolitical: Diversifying supply in a world where China controls nearly all of it is mission-critical.
âWhat we offer is a recycled, local, secure supply of the most critical metals with a really low carbon footprint,â Ahmad says.
The Purity Advantage
Then thereâs the product itself.
Cyclicâs rare earth oxides are cleaner, purer, and more consistent than whatâs typically available from mining.
Why? Because magnets contain only the most valuable rare earths and none of the radioactive contaminants (like thorium and uranium) often found in mined ores.
âWe probably produce the highest quality rare earth oxides in the market today,â Ahmad says. âNo radioactive materials. Very high-grade. And consistently hitting spec.â
Demand is skyrocketing.
âWe have a large volume of ask from the industry for what we produce,â Ahmad says. âWe have to run faster to be able to supply.â
The Supercool Takeaway
The low-carbon future is being built deep in the industrial core of the economy, in places few people ever see.
For Cyclic Materials, that means:
â
Unlocking critical materials from yesterdayâs machines
â
Building local, resilient supply chains
â
Reducing emissions, water use, and geopolitical risk
â
Delivering ultra-pure rare earths to power the next generation of electrification
The materials that power the future are already here.
Cyclic Materials has built the technology and the supply chain to bring them back.
Listen to this podcast episode on Apple, Spotify, YouTube, and all other platforms.
â
This Weekâs Supercool Sponsor

The Garbage Bag Gets an Upgrade.
Youâll take out the trash more than 8,000 times in your life. Might as well make it count and look good, too. Rubbish makes compostable, non-toxic, PFAS-free garbage bags with a sense of humor. (Yes, thereâs a new saying on every bag.) They remind you when youâre almost out, donate 10% of their bags to charity, and design for the circular economy.
â
Stat of the week: 90%
Thatâs how much of the worldâs rare earths China produces. Two decades ago, China saw the future and moved decisively, securing supply, scaling capacity, and leaving the West dependent. Thatâs what makes Cyclic Materials so vital and why rare earths are now front-page news.
Quote of the week:
We started the company in 2021. In 2024, we shipped our first ton of rare earth oxides. In the mining and metals industry, thatâs a speed record never before broken. So I think recycling will be the way to supply the critical metals into the market in the short term at a really fast pace versus other companies who are traditionally mining.
â
Urban mining isnât about recycling soda cans and water bottles.
Itâs about copper in old buildings. Gold in broken phones. Zinc in forgotten pipes.
Viewed through the lens of the circular economy, these materials arenât waste but feedstock for the supply chain.
Like Cyclic Materials for rare earth magnets, other companies are turning to the urban landscape to extract critical metals from products, buildings, and infrastructure past their prime.
The motivations are clear: secure supply, eliminate waste, declutter landfills, and decarbonize production.
Taiwan has emerged as a leader in the field. As is often the case, necessity drives innovation. The country plays a vital role in high-tech global supply chains but lacks the virgin resources to power its industries.
Urban mining has become a logical step and a foundation of Taiwanâs decarbonization strategy and economic resilience.
Solar Tech refines its raw materials from waste.
The Taiwanese company supplies high-purity metals for semiconductors, solar panels, and digital displays, sourced from its customersâ scrap. Old circuit boards, spent wafers, and discarded sputtering targets (materials used in thin films) are reclaimed, purified to 99.99%, and fed back into the supply chain.
With 80% of its inputs now coming from its own recycling stream, Solar Tech has built a circular industrial model at scale. Its proprietary technology refines eight high-value elements, from gallium to indium. In 2022, it recycled 247 metric tons of material and avoided more than 440,000 metric tons of carbon emissions.
Taiwanâs steelmakers donât just competeâthey collaborate to stay ahead.
Tung Ho Steel operates one of the largest urban mines on Earth. As a founding member of the Taiwan Steel Union, Tung Ho Steel partners with its peers to recycle hazardous byproducts from steel production. Together, they recover zinc oxide from dustâa substance that once threatened local ecosystems but now supplies a valuable industrial input.
Zinc, the fourth most-used metal on Earth and a key to the low-carbon economy, is refined and reused in coatings and batteries, reducing dependence on imports and cutting emissions.
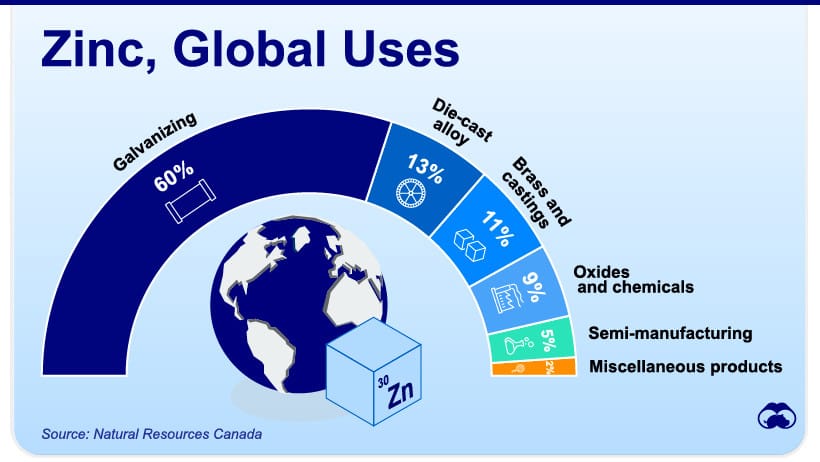
Zincâs primary use is in the galvanizing process, which protects iron and steel from rusting.
In 2021, Tung Ho Steel recycled over 50,000 tons of zinc oxide and avoided more than 47,000 tons of COâ.
â
Where Supercool Traveled This Week
Two podcasts:
Sustainably GeekyâWhatâs Cooler Than Being Cool with Josh Dorfman
The Samuele Tini Showâ ââWhy Your Climate Anxiety Is the Next Billion-Dollar Idea
â
Not yet subscribed to Supercool?
Click the button below for weekly updates on real-world climate solutions that cut carbon, boost the bottom line, and improve modern life.
đ